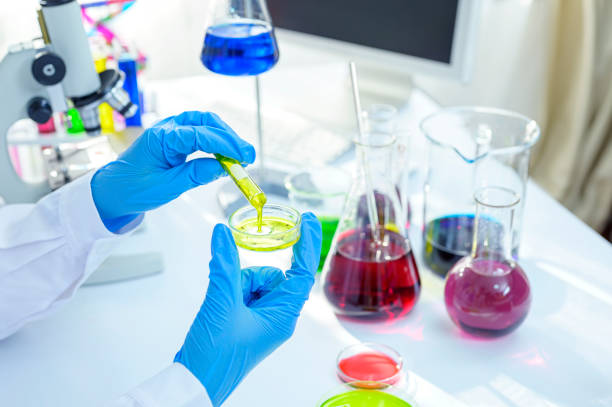
Oil Analysis
Oil Analysis: An Essential Tool for Machinery Health
Oil analysis is a critical preventive maintenance practice used to monitor the condition of machinery, engines, and hydraulic systems. By analyzing the properties of lubricants, oil analysis helps identify wear, contamination, and degradation issues before they lead to costly breakdowns or failures. This process is invaluable for industries that rely on heavy machinery, such as manufacturing, transportation, construction, and power generation.
Why Oil Analysis Matters
Lubricating oil serves multiple functions in mechanical systems: it reduces friction, dissipates heat, and protects against wear and corrosion. Over time, the oil itself can degrade, and contaminants like dirt, water, or metal particles can accumulate. Without timely intervention, these contaminants can damage the machine components, reduce efficiency, and eventually cause system failure.
Oil analysis provides early detection of these problems by identifying three key issues:
Oil Contamination: External substances such as dirt, water, fuel, or coolant can enter the oil, reducing its efficiency. Contamination can arise from various sources like poor seals, leaks, or environmental exposure. For example, water contamination can result in rust, while dirt can increase wear in metal components.
Oil Degradation: Over time, oil can break down due to heat, pressure, or chemical reactions. When oil degrades, its viscosity and lubrication properties are compromised. Degraded oil cannot protect machinery as effectively, leading to increased wear and overheating.
Wear Debris: As machinery operates, small metal particles are shed due to friction and wear. Monitoring these particles in the oil can indicate the health of internal components. For instance, elevated levels of iron or copper particles might signal wear in bearings, gears, or engine parts.
Key Oil Analysis Tests
Different tests are performed to assess the condition of the oil and the machine. Some of the most common tests include:
Viscosity Test: Viscosity measures the oil’s resistance to flow. It is one of the most critical properties, as it determines the oil’s ability to provide adequate lubrication. A change in viscosity may indicate oil degradation, contamination, or improper oil selection.
Spectrochemical Analysis: This test detects the presence and concentration of metal particles in the oil, providing insights into which machine components may be wearing. Each metal can correspond to specific machine parts; for example, aluminum may indicate wear in pistons, while bronze could indicate bushing wear.
Total Acid Number (TAN) and Total Base Number (TBN): These tests measure the oil’s acidity or alkalinity. TAN is crucial for monitoring oil oxidation and contamination by acids, while TBN measures the oil’s ability to neutralize acids, particularly in engine oils.
Water Content Analysis: Water in oil can lead to rust, corrosion, and a breakdown in lubrication properties. Water content can be measured using techniques like Karl Fischer titration or infrared spectroscopy.
Particle Count: This test measures the size and quantity of particles in the oil, often conducted using an automatic particle counter. High particle counts can indicate contamination or excessive wear in the system.
Benefits of Oil Analysis
The primary advantage of oil analysis is that it allows for condition-based maintenance rather than reactive or scheduled maintenance. By identifying issues early, companies can avoid unplanned downtime, reduce repair costs, and extend machinery life. Other benefits include:
Improved Reliability: Regular oil analysis ensures machinery is running efficiently and reduces the risk of sudden failures.
Cost Savings: Preventive measures are always more cost-effective than emergency repairs or replacements.
Optimized Maintenance Scheduling: Oil analysis helps determine the right time for oil changes, reducing unnecessary oil changes while ensuring that machinery is properly lubricated.
Environmental Benefits: Prolonging the life of lubricating oil through regular monitoring reduces oil consumption and disposal, which is better for the environment.
Conclusion
Oil analysis is a powerful diagnostic tool that ensures the long-term health and efficiency of mechanical systems. By understanding oil contamination, degradation, and wear debris, businesses can make informed maintenance decisions, minimize equipment downtime, and ultimately protect their investments. Regular oil analysis helps transform maintenance strategies from reactive to proactive, ensuring machines run smoothly and reliably for longer periods.